What is Laser Welding
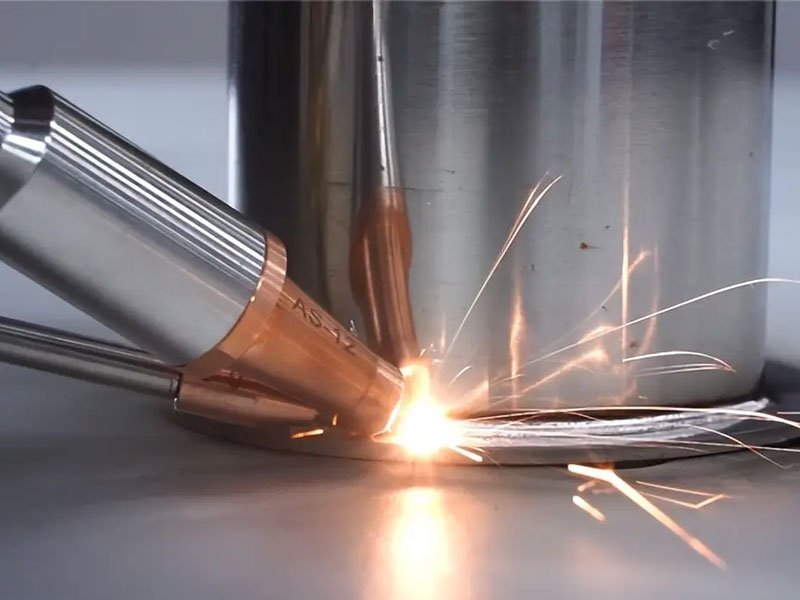
In modern manufacturing, precision and efficiency are of the utmost importance. One technology that has revolutionized the way we join materials is laser welding. This advanced welding technology has become a cornerstone of industries ranging from automotive to aerospace and even precision medical device manufacturing.
What exactly is laser welding? And why is it so popular? Let’s take a deeper look.
What is Laser Welding?
Laser welding is a process that uses a highly focused beam of light—a laser—to join materials together. The laser beam delivers an intense amount of energy to a small, precise area, melting the material and creating a strong weld as it cools. Unlike traditional welding methods, which rely on electric arcs or gas flames, laser welding offers unparalleled precision, speed, and control.
The laser used in welding is typically generated by a solid-state, fiber, or CO2 laser source. These lasers can produce beams with wavelengths that are easily absorbed by metals, making them ideal for welding applications.
How Does Laser Welding Work?
- Beam Generation: A laser source generates a coherent beam of light, which is then directed through a series of mirrors or fiber optics to the workpiece.
- Focusing the Beam: The laser beam is focused onto the material using a lens or specialized optics. This creates a tiny, high-energy spot that can reach temperatures high enough to melt the material.
- Material Interaction: When the laser beam hits the material, its energy is absorbed, causing the material to melt and form a molten pool. In some cases, a shielding gas (such as argon or nitrogen) is used to protect the weld from oxidation and contamination.
- Cooling and Solidification: As the laser beam moves along the joint, the molten material cools and solidifies, creating a strong, precise weld.
Types of Laser Welding
- Conduction Welding: In this method, the laser beam heats the material just enough to melt it, without vaporizing it. This results in a smooth, shallow weld with minimal distortion. It’s ideal for thin materials or applications where aesthetics are important.
- Keyhole Welding: This technique uses higher laser power to create a deep, narrow vapor channel (or “keyhole”) in the material. The molten material flows around the keyhole, creating a deep and strong weld. Keyhole welding is commonly used for thicker materials or when high structural integrity is required.
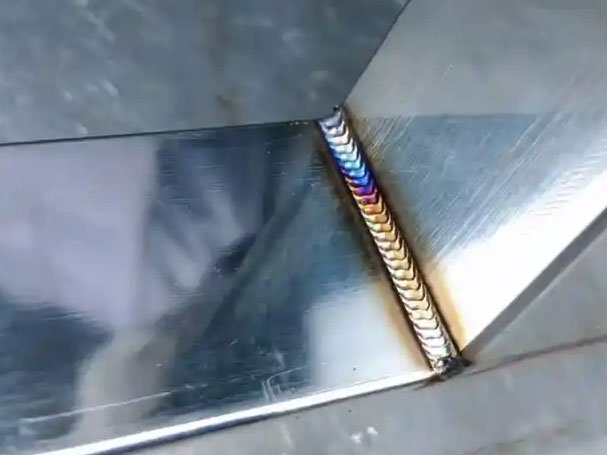
Advantages of Laser Welding
- Precision: The focused laser beam allows for extremely precise welds, even on small or complex parts.
- Speed: Laser welding is significantly faster than many conventional welding techniques, increasing productivity.
- Minimal Heat Affected Zone (HAZ): The concentrated heat input reduces the risk of warping or damaging surrounding areas.
- Versatility: Laser welding can be used on a wide range of materials, including metals, plastics, and even dissimilar materials.
- Automation-Friendly: The process is easily integrated into automated systems, making it ideal for high-volume production.
Applications of Laser Welding
- Automotive: For welding car body components, batteries for electric vehicles, and exhaust systems.
- Aerospace: For joining lightweight materials like titanium and aluminum in aircraft structures.
- Medical Devices: For creating precise, clean welds in surgical instruments and implants.
- Electronics: For welding small, delicate components in smartphones, sensors, and other devices.
- Jewelry: For creating intricate, high-quality welds in precious metals.
Challenges and Considerations
While laser welding is a powerful tool, it’s not without its challenges. The initial cost of laser welding equipment can be high, and the process requires skilled operators and precise control of parameters like laser power, speed, and focus. Additionally, certain materials, such as highly reflective metals, can be more difficult to weld with lasers.
The Future of Laser Welding
As technology continues to advance, laser welding is becoming even more accessible and versatile. Innovations in laser sources, such as fiber lasers, are making the process more efficient and cost-effective. Additionally, the integration of artificial intelligence and machine learning is enabling smarter, more adaptive welding systems.
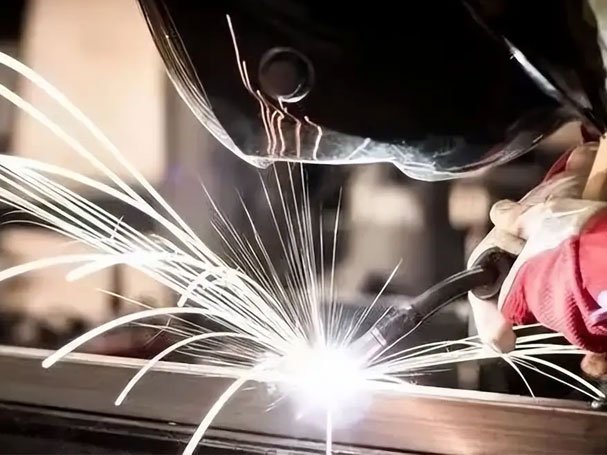
Conclusion
Laser welding is a game-changing technology that offers unmatched precision, speed, and versatility. Whether you’re building a car, a plane, or a life-saving medical device, laser welding is likely playing a crucial role behind the scenes. As the technology continues to evolve, its applications—and its impact on manufacturing—will only grow.
FAQ
What materials can be laser welded?
Laser welding can be used on a variety of materials, including metals like steel, aluminum, titanium, and copper, as well as plastics and even dissimilar materials. However, highly reflective metals (e.g., copper and aluminum) may require specialized laser settings
What is the difference between laser welding and traditional welding?
The key difference is the heat source: laser welding uses a focused laser beam, while traditional welding relies on electric arcs or gas flames.
Laser welding offers greater precision, faster speeds, and less distortion compared to traditional methods, making it ideal for high-tech and delicate applications.
Is laser welding stronger than traditional welding?
Laser welding can produce stronger and more precise welds compared to traditional methods, especially for thin materials or complex joints. However, the strength of the weld depends on factors like material type, laser settings, and joint design.
What is the cost of laser welding?
The cost of laser welding varies depending on the equipment, materials, and complexity of the project. While initial setup costs can be high due to the price of laser systems, the process often reduces long-term costs through faster production, less material waste, and minimal post-weld processing.
Can laser welding be automated?
Yes, laser welding is highly suitable for automation. It is often integrated into robotic systems for high-volume production, ensuring consistent quality, precision, and efficiency in industries like automotive and electronics manufacturing.
What are the limitations of laser welding?
- High initial equipment costs
- Difficulty welding highly reflective materials (e.g., copper, aluminum) without specialized settings
- Requires precise alignment and control of parameters
- Not ideal for very thick materials in some cases
What is the difference between laser welding and laser cutting?
Laser welding uses a focused laser beam to join materials by melting them, while laser cutting uses the same technology to cut through materials by vaporizing or melting them along a defined path. Both processes use high-energy lasers but serve different purposes in manufacturing.